Discover how plastic extrusion boosts production efficiency
Discover how plastic extrusion boosts production efficiency
Blog Article
Understanding the Fundamentals and Applications of Plastic Extrusion in Modern Production
In the realm of contemporary production, the strategy of plastic extrusion plays an instrumental function. Unwinding the principles of this process reveals the true adaptability and capacity of plastic extrusion.
The Principles of Plastic Extrusion Process
While it might show up complicated, the basics of the plastic extrusion procedure are based on relatively straightforward principles. It is a production process wherein plastic is melted and after that shaped right into a continual profile via a die. The raw plastic product, typically in the type of pellets, is fed right into an extruder. Inside the extruder, the plastic is subjected to warm and stress, triggering it to thaw. The liquified plastic is then compelled with a designed opening, understood as a die, to form a long, continuous product. The extruded product is cooled and afterwards cut to the preferred length. The plastic extrusion procedure is thoroughly used in various markets due to its versatility, performance, and cost-effectiveness.
Various Sorts Of Plastic Extrusion Techniques
Building upon the basic understanding of the plastic extrusion process, it is necessary to explore the various methods involved in this manufacturing approach. In contrast, sheet extrusion produces large, level sheets of plastic, which are typically additional refined into items such as food packaging, shower curtains, and vehicle parts. Recognizing these techniques is crucial to making use of plastic extrusion successfully in contemporary production.

The Role of Plastic Extrusion in the Automotive Industry
An overwhelming bulk of parts in modern lorries are items of the plastic extrusion process. This process has revolutionized the auto market, transforming it into a much more effective, cost-effective, and adaptable production sector. Plastic extrusion is mainly utilized in the manufacturing of numerous car elements such as bumpers, grills, door panels, and dashboard trim. The procedure gives an attire, regular output, enabling makers to generate high-volume get rid of fantastic precision and minimal waste. The agility of the extruded plastic components adds to the general reduction in vehicle weight, boosting fuel efficiency. The resilience and resistance of these components to warm, chilly, and effect boost the longevity of cars. Thus, plastic extrusion plays a pivotal role in automotive manufacturing.
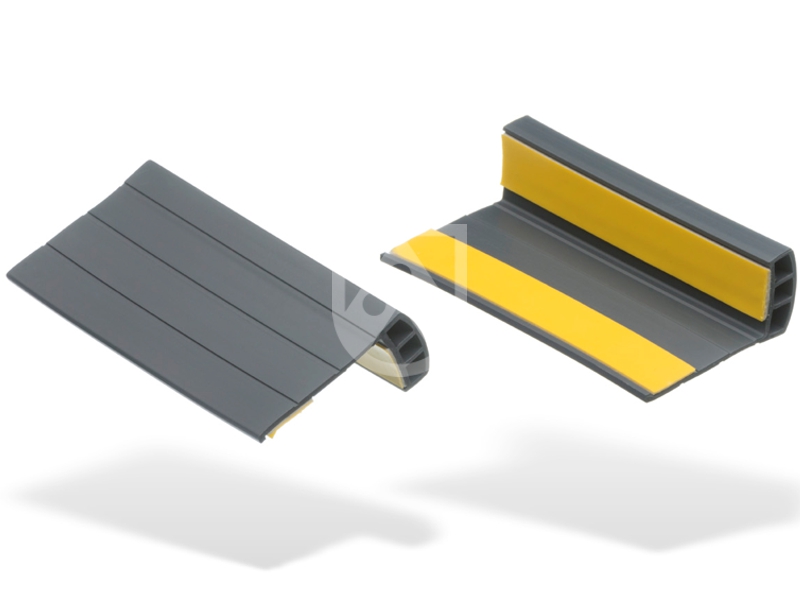
Applications of Plastic Extrusion in Customer Product Manufacturing
Past its considerable impact on the automotive market, plastic extrusion verifies similarly effective in the realm of durable goods making. This procedure find is essential in producing a vast range of products, from food packaging to house appliances, toys, and even clinical tools. The adaptability of plastic extrusion allows manufacturers to create and generate intricate shapes and dimensions with high accuracy and efficiency. In addition, because of the recyclability of lots of plastics, squeezed out parts can be recycled, lowering waste and price. The adaptability, flexibility, and cost-effectiveness of plastic extrusion make it a preferred choice for many customer products producers, contributing substantially to the industry's growth and advancement. The environmental ramifications of this widespread usage require careful consideration, a subject to be discussed better in the subsequent section.
Environmental Effect and Sustainability in Plastic Extrusion
The pervasive use plastic extrusion in manufacturing invites scrutiny of its environmental effects. As a procedure that frequently uses non-biodegradable products, the environmental influence can be considerable. Power usage, waste production, and carbon emissions are all issues. Industry developments are raising sustainability. Reliable equipment decreases power use, while waste administration systems recycle scrap plastic, decreasing resources needs. Furthermore, the development of eco-friendly plastics offers a much more eco-friendly option. In spite of these improvements, further technology is see here required to minimize the environmental impact of plastic extrusion. As culture leans towards sustainability, makers must adapt to remain feasible, emphasizing the significance of continual study and improvement in this field.
Conclusion
To conclude, plastic extrusion plays an important function in modern-day manufacturing, especially in the automotive and customer products fields. Its versatility permits the production of a vast array of elements with high accuracy. Its potential for reusing and development of naturally degradable materials uses a promising opportunity in the direction of lasting practices, consequently attending to environmental concerns. Understanding the basics of this procedure is key to maximizing its advantages and applications.
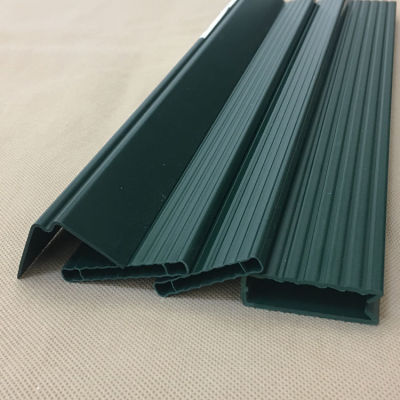
The plastic extrusion procedure is thoroughly used in various industries due to its convenience, cost-effectiveness, and effectiveness.
Structure upon the fundamental understanding of the plastic extrusion process, it is required to explore the different methods included in this manufacturing technique. plastic extrusion. In comparison, sheet extrusion produces huge, flat sheets of plastic, which are normally further refined right into products such as food packaging, shower curtains, and vehicle parts.A frustrating majority of parts in modern-day vehicles are products Visit Website of the plastic extrusion process
Report this page